Ceramic Vacuum Filter
Ceramic Vacuum Filter
Ceramic Vacuum filter ( Vacuum disc filter ) is a new generation of high efficiency and energy-saving solid-liquid separation system. The basic principle resembles a common disk vacuum filter, but the key difference is that the ceramic filter operates with porous ceramic filter disks as filtering medium, which allows only water going through the filter disks but not solids or gas. The pore size of the ceramic filter plate is usually 1-5 microns (1.5-2.0 microns is the most commonly used). Such micropores can produce strong capillary action.As a result, solid particles in the slurry are adsorbed on the outer surface of the disks and dried to low moisture content.
Features
- Large processing capacity and apparent energy-saving effect.
- It adopts PLC program for automatic control, automatic feeding and automatic cleaning, which reduces the labor cost of system operation.
- It has an automatic fault alarm system, fault screen display function, high and low liquid level alarm display, and automatic removal or shutdown manual processing.
- The structure is reasonable, the work is reliable, the main transmission parts adopt a maintenance-free design, and the tank body adopts stainless steel.
- The water content of the filtered and dehydrated material is very low, which can significantly reduce transportation costs and losses.
- Because the filtrate is clear, it can be reused, reducing emissions, in line with the current environmental protection trend of cleaner production.
Working principle
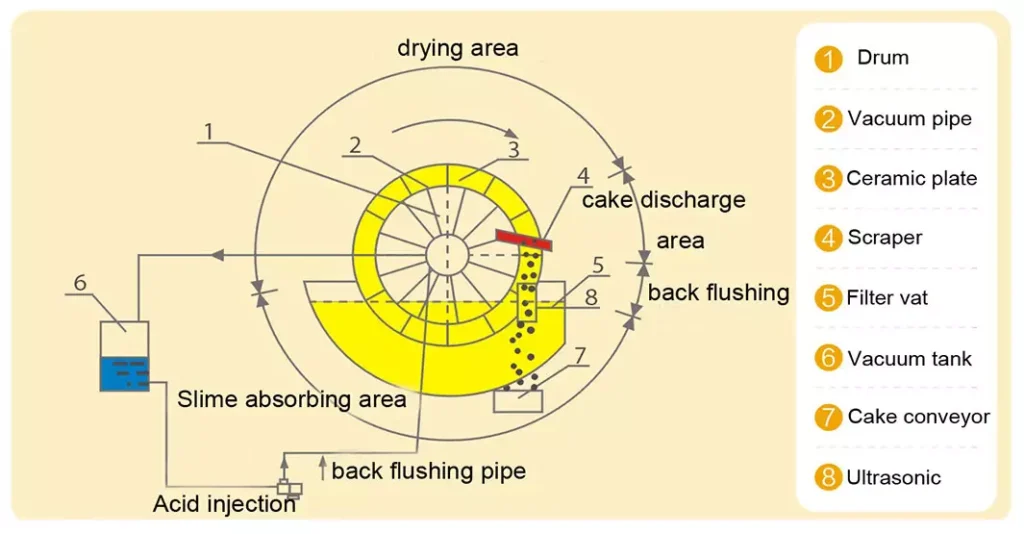
When the microporous plates are submerged into the pulp, filtering elements remove the liquid in contact with their surface due to the capillary effect. The vacuum pump applies the driving force to move the slurry liquor through the ceramic elements and into filtrate pipes. On the outer surface of the elements the filter cake forms rapidly, the effective design of the sectors prevents the passage of fine solids and air through the filtrate system.
As the ceramic filter elements rotate above the slurry level, the capillary action within the ceramic elements continuously removes the residual moisture from the filter cake. This highly efficient dewatering process produces low final cake moistures at minimum operation and maintenance costs, compared to the trade-Dtional dewatering systems
The ceramic scraper knives cleanly and effectively shave through the formed and dewatered filter cake. A layer of solids remain on the filter element providing protection from the mechanical abrasive action, This design results in reduction of the maintenance costs and increase of the service life of the ceramic filters.
At this stage, clean plant water is applied to the back wash the internals of the ceramic filter elements and to remove the residual filter cake. This process effectively cleans both the ceramic sectors to maintain maximum filtration rates and the lowest final cake moisture. The pressure and flow of the wash water during this regeneration operation automatic control under.
Video
Technology
Model | Filter Surface | Filter Plate Discs (discs) | Compressed Air Consumption (m³) | Outlet Capacity (t/h) | Installed power (kw) | Weight (kg) | Length*Width*Height (mm) |
WKL-12 | 12 | 3 | 0.7 | 2 | 12.15 | 2700 | 2800*2300*2550 |
WKL-15 | 15 | 4 | 0.8 | 2.5 | 16.25 | 4500 | 3150*2300*2550 |
WKL-24 | 24 | 6 | 1 | 4 | 18.75 | 6000 | 3750*2300*2550 |
WKL-30 | 30 | 8 | 1.4 | 5 | 18.75 | 8000 | 4350*2300*2550 |
WKL-40 | 40 | 11 | 2.5 | 6 | 24.55 | 9500 | 4950*2300*2550 |
WKL-50 | 50 | 13 | 2.7 | 7 | 35.9 | 12000 | 5550*2300*2550 |
WKL-60 | 60 | 16 | 3 | 8 | 35.9 | 15000 | 6450*2300*2550 |
WKL-75 | 75 | 20 | 3.2 | 10 | 48 | 18000 | 7350*2300*2550 |
WKL-90 | 90 | 24 | 3.84 | 12 | 54 | 21000 | 8550*2300*2550 |